Last week I had the pleasure of attending a demonstration of the University of Virginia’s replica wooden common press:
The common press at the University of Virginia.
The earliest printing presses in Europe, from the time of Johannes Gutenberg and his associates Peter Schöffer and Johann Fust, were constructed primarily out of wood. Using similar technologies as contemporary agricultural presses (for winemaking, papermaking, olive oil extraction, and linen pressing), these 15th century printing presses used a wooden screw to lower a heavy wooden plate onto a bed holding cast metal type. The screw was turned by pulling a lever, or "bar" (also called the Devil's Tail ;-). Wooden common presses remained in use until the early 1800s, when iron handpresses and new types of cylinder and platen presses were developed.
Josef Beery demonstrating UVA's wooden common press.
UVA’s common press was constructed in the 1970s, as a result of research at the Smithsonian Institution on the "Franklin" common press. It is on display in the Harrison Small Building’s South Gallery. Though the bar is kept locked for safety most of the time, you can still walk right up to the press and examine much of its design and function. Occasionally, folks associated with UVA’s Rare Book School offer working demonstrations.
The session I attended last week was lead by Josef Beery ~ book designer, letterpress printer, woodcut artist, papermaker, educator, and cofounder of the Virginia Arts of the Book Center in Charlottesville. A practitioner of the printing arts for many decades, Beery is a perfect guide to the history and use of this fascinating press.
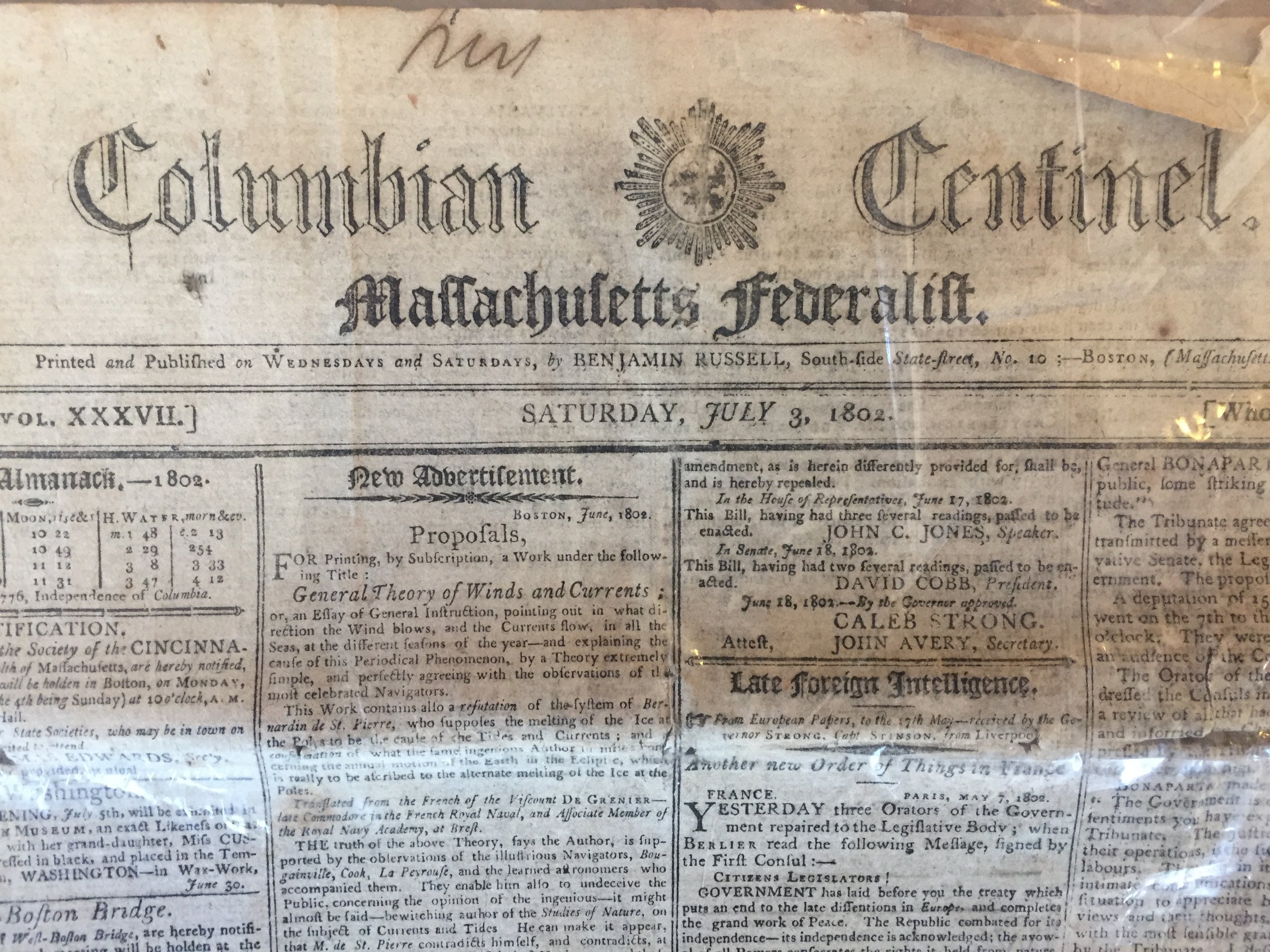
When you finish marveling at the wooden common press, head downstairs to the Albert & Shirley Small Special Collections Library. A highlight of the Library’s wonderful collection of rare books and manuscripts (including significant holdings in the history of books and printing) is a rare first-printing of the Declaration of Independence, printed the night of July 4th by John Dunlap. It’s on permanent display along with many other early printings of the document (the world’s most comprehensive collection of these) near the Library’s entrance.
If you're ever in the vicinity of Charlottesville, Virginia, don't miss this chance to see the common press, the Declaration of Independence, and many other artifacts of printing-circa-1776!
* For more information on early American printing history, visit the American Printing History Association (APHA) website.
* To follow the fascinating process of reconstructing a wooden common press, visit Seth Gottlieb's blog post series at APHA.
* Watch Josef Beery demonstrating the traditional method of using ink balls to apply ink to the type on a common press: